ANSYS-CFX Simulation and Experimental Studies on Centrifugal Pump Impeller Design: Performance Effects Using Corrosive and Non-corrosive Resources
Keywords:
ANSYS, Centrifugal pump, Impeller, Performance curve, Computational fluid dynamics, BladeGen, Finite element analysis, Blade angleAbstract
Corrosive fluids, namely saline water, hydrochloric acid and methanol and non-corrosive fluids, namely, water, gasoline and kerosene can be tested for efficiency and reliability on an existing H47 centrifugal pump impeller’s performance. To analyze the pump performance, ANSYS student version 2022 software was used – wherein; head rise (H), pump speed (N), discharge rate (Q) and inlet pressure of 20-120m, 2000rpm, 144m3/h and 0 atm were respectively specified as initial and boundary conditions in the computational fluid dynamics (CFD) tool. CFD for inlet and exit blade angles of 35o, 38o, 41o and 47o, 50o, 53o were respectively simulated for all fluid type using a 7-bladed impeller to obtain contour plots and pressure and velocity distribution results of the analysis. It was deduced that the overall efficiency of the centrifugal pump depends on the outlet blade angle and fluid type, while the power used rises with both inlet and outlet blade angles. Further studies should be channeled towards analyzing the variations in N, Q, H, impeller blade number (Z) and its width, for this particular type of impeller.
Downloads
References
A. S. Prasad, B. L. Rao, A. Babji, and P. K. Babu, “Static and dynamic analysis of a centrifugal pump impeller,” Int. J. Sci. Eng. Res., vol. 4, no. 10, pp. 966–971, 2013, [Online]. Available: http://www.ijser.org.
Q. Zhang, H. Zhou, Q. Gao, and Z. Cui, “Analysis of effects of impeller inlet width on the performance of centrifugal pump,” J. Chem. Pharm. Res., vol. 6, no. 5, pp. 2078–2081, 2014, [Online]. Available: www.jocpr.com.
J. Chen, W. Shi, and D. Zhang, “Influence of blade inlet angle on the peformance of a single blade centrifugal pump,” Eng. Appl. Comput. Fluid Mech., vol. 15, no. 1, pp. 462–475, 2021, doi: 10.1080/19942060.2020.1868341.
X. Han, Y. Kang, D. Li, and W. Zhao, “Impeller optimized design of the centrifugal pump: A numerical and experimental investigation,” Energies, vol. 11, no. 1444, pp. 1–21, 2018, doi: 10.3390/en11061444.
K. K. Yadav and V. K. Gahlot, “Performance improvement of mixed flow pump impeller through CFD analysis,” Int. J. Res. Eng. Technol., vol. 4, no. 7, pp. 243–247, 2015, [Online]. Available: http://www.ijret.org.
S. Susilo and A. Setiawan, “Analysis of the number and angle of the impeller blade to the performance of centrifugal pump,” EUREKA Phys. Eng., vol. 5, pp. 53–61, 2021, doi: 10.21303/2461-4262.2021.002001.
E. C. Bacharoudis, A. E. Filios, M. D. Mentzos, and D. P. Margaris, “Parametric study of a centifugal pump impeller by varying the outlet blade angle,” Open Mech. Eng. J., vol. 2, pp. 75–83, 2008.
H. Ding, Z. Li, X. Gong, and M. Li, “The influence of blade outlet angle on the performance of centrifugal pump with high specific speed,” Vacuum, vol. 159, pp. 239–246, 2019, doi: 10.1016/j.vacuum.2018.10.049.
A. A. Adeniyi and O. D. Komolafe, “Performance analysis of an experimental centrifugal pump,” Niger. J. Technol., vol. 22, no. 2, pp. 149–155, 2014, doi: 10.4314/njt.v33i2.2.
S. N. Shukla and J. T. Kshirsagar, “Numerical experiments on a centrifugal pump,” in Proceedings Sciences: Fluids Engineering Division Summer Meeting, 2009, pp. 709–719, doi: 10.1115/FEDSM2002-31176.
N. Mohamed et al., “Stress analysis of various designs of centrifugal pump impellers using finite element method,” J. Eng. Technol. Adv., vol. 7, no. 1, pp. 36–46, 2022, doi: 10.35934/segi.v7i1.48.
M. Ashri, S. Karuppanan, S. Patil, and I. Idris, “Modal analysis of a centrifugal pump impeller using finite element method,” in MATEC Web of Conferences, 2014, vol. 13, no. 04030, pp. 1–5, doi: 10.1051/matecconf/20141304030.
S. Rajendran and K. Purushothaman, “Analysis of a centrifugal pump impeller using ANSYS-CFX,” Int. J. Eng. Res. Technol., vol. 1, no. 3, pp. 1–6, 2012, [Online]. Available: www.ijert.org.
R. S. Muttali, S. Agrawal, and H. Warudhkar, “CFD simulation of centrifugal pump impeller using ANSYS-CFX,” Int. J. Innov. Res. Sci. Eng. Technol., vol. 3, no. 8, pp. 15553–15561, 2014, doi: 10.15680/IJIRSET.2014.0308066.
G. R. H. A. Elyamin, M. A. Bassily, K. Y. Khalil, and M. S. Gomaa, “Effect of impeller blades number on the performance of a centrifugal pump,” Alexandria Eng. J., vol. 58, pp. 39–48, 2019, doi: 10.1016/j.aej.2019.02.004.
M. N. Idris and I. U. Usman, “Design studies using corrosive and non-corrosive materials to improve on reliability and efficiency of an impeller of a centrifugal pump,” in The Electrochemical Society (ECS) Meeting Abstracts, Volume MA2022-02 Z01: General Student Poster Session, 2022, vol. MA2022-02, no. 64, pp. 2345–2345, doi: 10.1149/MA2022-02642345mtgabs.
I. U. Usman and M. N. Idris, “Experimental studies and designs using corrosive and non-corrosive materials to improve on reliability and efficiency of an impeller of a centrifugal pump,” in CHE 599 Proposal Presentation 2021/2022 Session, 2021, pp. 1–1, [Online]. Available: https://www.researchgate.net/publication/356894529.
M. Murakami, K. Kikuyama, and E. Asakura, “Velocity and pressure distributions in the impeller passages of centrifugal pumps,” in Symposium on Measurement Methods in Rotating Components of Turbomachinery, Gas Turbine and Fluids Engineering Conference, New Orleans, La, 1980, vol. 102, pp. 420–420, [Online]. Available: https://fluidsengineering.asmedigitalcollection.asme.org.
X. Jia, B. Cui, Z. Zhu, and X. Yu, “Numerical investigation of pressure distribution in a low specific centrifugal pump,” J. Therm. Sci., vol. 27, pp. 25–33, 2018, doi: 10.1007/s11630-018-0980-9.
Q. Li, S. Li, P. Wu, B. Wuang, and D. Wu, “Investigation on reduction of pressure fluctuation for a double-suction centifugal pump,” Chinese J. Mech. Eng., vol. 34, no. 12, pp. 1–18, 2021, doi: 10.1186/s10033-020-00505-8.
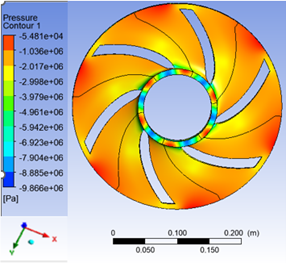
Downloads
Published
How to Cite
Issue
Section
ARK
License
Copyright (c) 2023 Abdulhalim Abubakar

This work is licensed under a Creative Commons Attribution 4.0 International License.
Copyright on any article in the International Journal of Engineering and Applied Physics is retained by the author(s) under the Creative Commons license, which permits unrestricted use, distribution, and reproduction provided the original work is properly cited.
License agreement
Authors grant IJEAP a license to publish the article and identify IJEAP as the original publisher.
Authors also grant any third party the right to use, distribute and reproduce the article in any medium, provided the original work is properly cited.